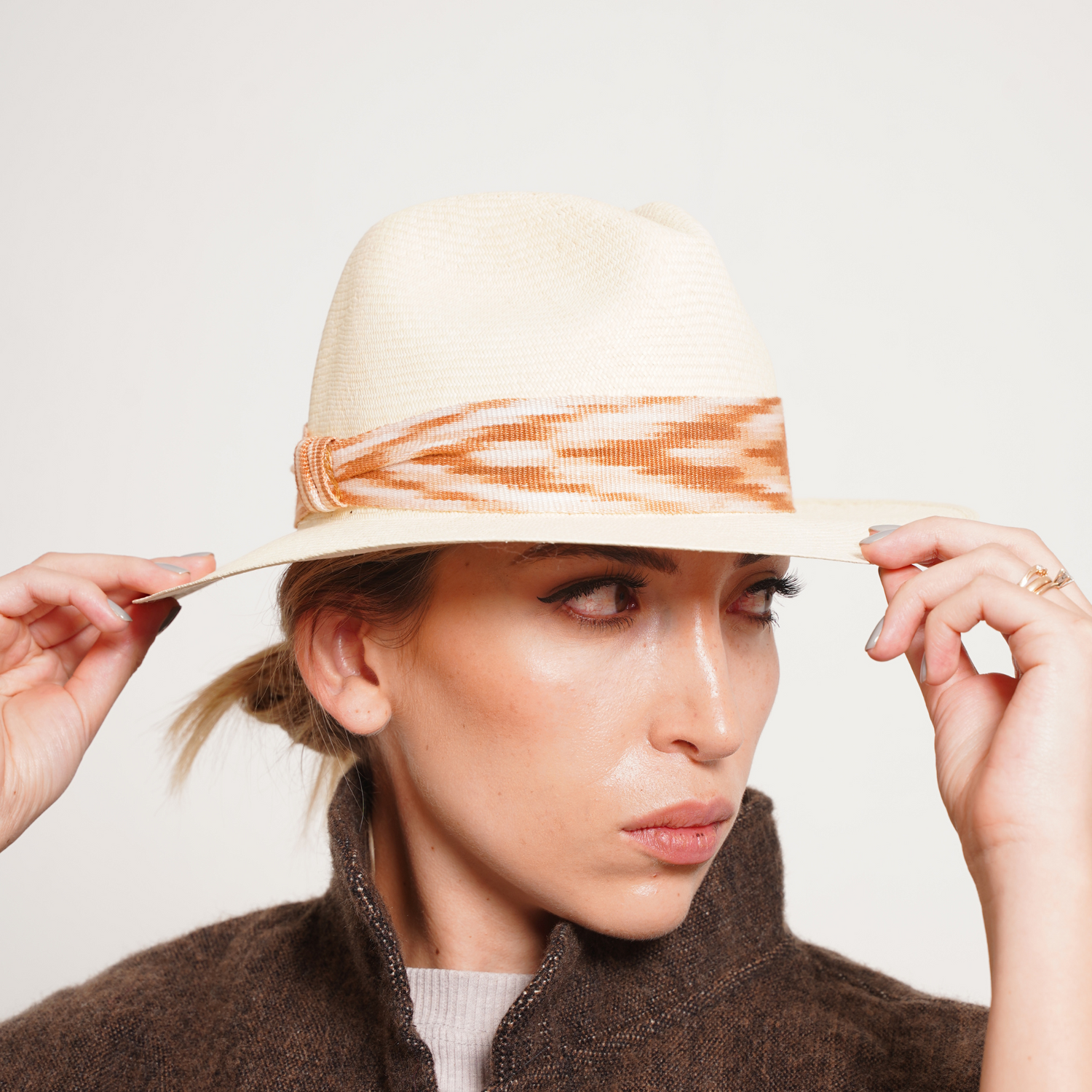
Handcrafted by artisans from Ecuador
Made from the fibers of the toquilla palm, which grows exclusively on the coast of Ecuador.
Making a Panama Hat is intricate and time-consuming, and it has been passed down through generations of artisans. It can take up to three weeks to complete a single hat.
To begin, the artisans carefully harvest the toquilla palm leaves and boil them in water to soften the fibers. They then split the fibers into very fine strands, which they weave together into a thin, flexible fabric. It takes around two to three weeks to make one of these pieces.
Once the basic shape of the hat has been formed, the artisans begin the process of adding the intricate decorative details that make each hat unique.
Throughout the process, the artisans rely on traditional techniques and tools, such as wooden blocks and knives, that have been used for generations. The finished product is a masterpiece of craftsmanship, full of detail, that tells a story of Ecuador's rich cultural heritage.
Panama Hats are not only beautiful, but they are also practical. The toquilla palm fibers used to make the hats are lightweight and breathable, making them perfect for hot and humid climates.
A unique handcrafted process
Sourcing the Finest Straw
The process starts with sourcing the highest quality straw to create a genuine Panama hat. The straw used is derived from the leaves of the Toquilla palm tree, which grows abundantly in coastal regions of Ecuador. Skilled artisans carefully select the most suitable palm leaves based on their color, flexibility, and strength. The type of straw chosen will determine the hat's quality and durability.
Preparing the Straw
The selected palm leaves are boiled in water and left to dry under the warm Ecuadorian sun. This process helps soften the straw and makes it easier to work with. The leaves are then split into fine strands, further sorted by size and thickness. The straw is now ready to be transformed into a beautiful hat.
Weaving the Brim and Crown
With nimble fingers and years of expertise, skilled artisans begin the intricate process of weaving the hat's brim and crown. They use a technique called "toquilla straw weaving," where the straw strands are delicately intertwined to create a tight, intricate pattern. The weaver patiently works their way around the circular molds, carefully shaping the brim and crown to the desired size and style. This process requires precision and attention to detail, ensuring a consistent weave throughout.
Blocking and Shaping
Once the weaving is complete, the hat undergoes a process known as blocking. The hat is placed on a wooden block and moistened with steam to make it pliable. Skilled craftsmen meticulously shape the hat using their hands, specialized tools, and sometimes even their own breath to create the perfect form. They work diligently to achieve the desired curvature of the brim and crown, giving the hat its distinctive shape.
Finishing Touches and Personalization
After the hat is shaped, it goes through several finishing touches. Excess straw ends are trimmed, and the edges of the brim are carefully smoothed. Artisans then add their personal touch, incorporating decorative elements such as ribbons, bands, or intricate designs.
Quality Control and Finale
Before a Panama hat is deemed complete, it undergoes a meticulous quality control process. Expert eyes inspect every detail, ensuring the hat meets the highest standards of craftsmanship. The final step involves steaming the hat once again to set its shape and enhance its durability. The hat is then gently brushed to remove any loose fibers, making it ready for packaging and delivery.
The entire process of crafting a Panama hat is a labor of love that takes around three weeks to complete. The timeline can vary depending on factors such as the complexity of the design, the skill of the weaver, and even the weather conditions, as the straw needs sufficient drying time. Each hat is a testament to the rich cultural heritage and artisanal traditions of Ecuador, where master craftsmen dedicate themselves to creating wearable works of art.








